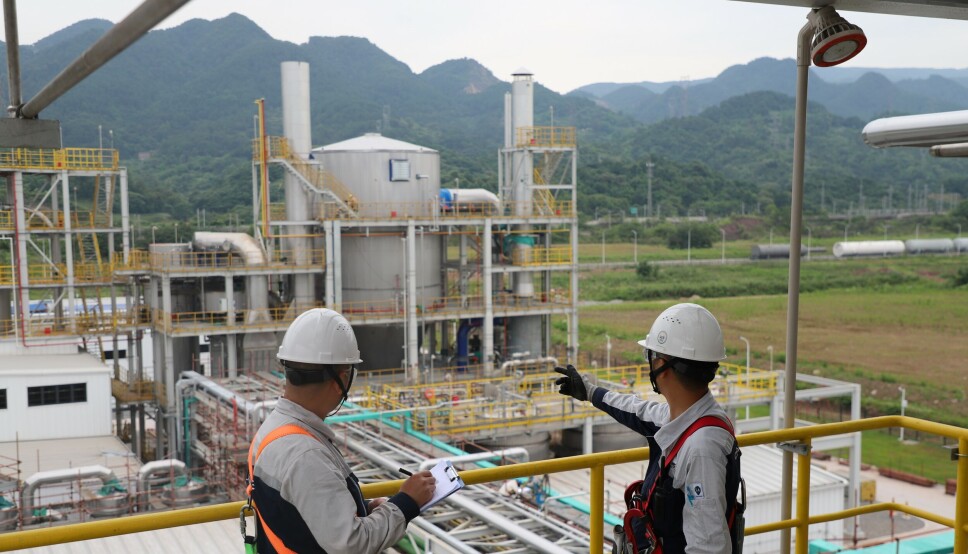
Gas-to-feed plant switched on in China
Calysseo facility will produce 20,000 tonnes of protein per year for aquaculture
The world’s first industrial-scale facility to produce FeedKind, a protein ingredient made from microbes that reproduce in a fermenter and feed off methane (natural gas), has switched on.
Calysseo, a joint venture between animal nutrition company Adisseo and protein innovator Calysta, will initially produce 20,000 tonnes of protein per year from the facility in Chongqing, China. With start-up operations complete, the fermenter will become world’s largest single cell protein production facility.
First deliveries of FeedKind Aqua will be made to customers soon, making it the first alternative fermented protein to address the fish farm feed sector at scale, said Calysseo.
'A new era'
FeedKind requires no agricultural land and very little water. Adisseo chief executive Jean-Marc Dublanc said: “Food security has increasingly come under the spotlight in recent months, but we are now entering a new era of sustainable food production.
“Calysseo brings to the market a new way of making high-quality protein – and does so using a naturally-occurring microbe that makes the resulting protein non-GMO, something that is increasingly demanded through the supply chain.
“We have a long-running commitment to improving the security and sustainability of the feed ingredient market and Calysseo fulfils a significant part of that pledge. We will provide Chinese customers with a reliable, domestically available supply of protein that meets their specific needs; produced in China for China.
“We are looking forward to working with our customers as they begin to integrate this product into their supply chains.”
Technology developed in UK
The microbial protein is produced via a natural fermentation, which takes place inside a novel high-capacity u-loop reactor patented by Calysta, which developed its technology on Teesside in northeast England from a Norwegian concept dating from the 1980s.
Calysseo said FeedKind answers an increasing need for a sustainable source of protein to meet the demands of a growing global population coupled with increased concerns about preserving biodiversity.
The Chongqing facility will produce FeedKind Aqua for use in fish farming, allowing farmers to replace fishmeal and soy. Initially, production will be available for use in China, the world’s largest aquaculture market.
Hyper-scaling
Dr Alan Shaw, the co-founder, chief executive and president of Calysta said: “We have spent the last 10 years perfecting our technology and it is exciting to have successfully switched on the world’s first industrial-scale alternative protein fermenter. This is a huge step as we aim to help make the world more food secure.
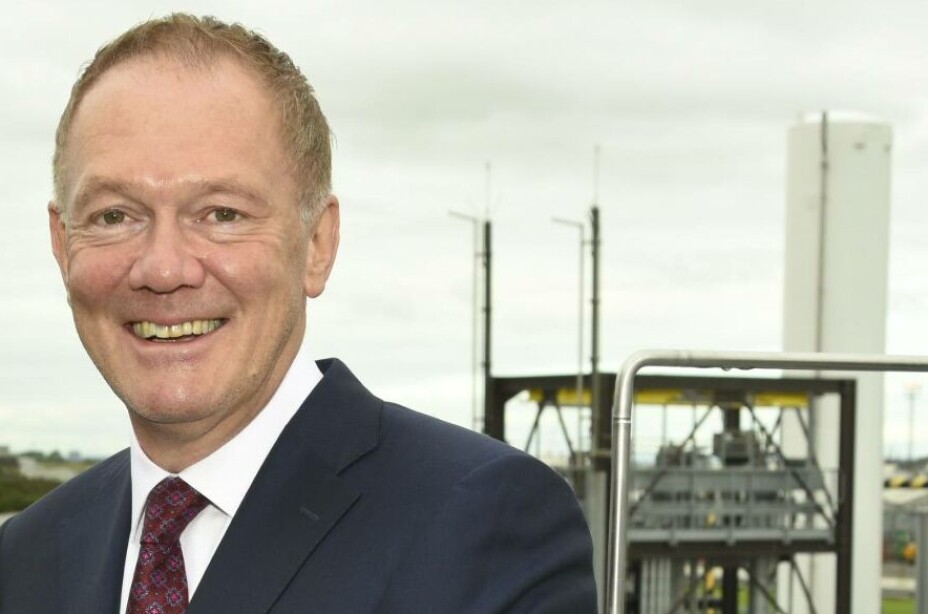
“Cellular agriculture, where protein is grown in a controlled environment, is key to helping the world meet its future food needs and we are proud to be taking the first steps on our journey to hyper-scaling this technology with Adisseo, who we look forward to working with for many years to come.
“This is an exciting time for Calysta as a whole, as we continue to work on bringing a host of additional protein ingredients for food and feed applications to market.”
On schedule
The Calysseo team had to overcome substantial challenges at Chongqing, with Covid restrictions in place throughout the build, said the company. Despite this, construction completed on schedule, and switching the fermenter on means production is now under way.
Pierre Casamatta, co-managing director of Calysseo, added: “We are doing something that has never been achieved before at scale, so I’m incredibly proud of our team to have completed the build on schedule and move so smoothly to successfully switching the fermenter on.”
Calysseo said FeedKind Aqua has been validated over several years following extensive trials across several aquaculture species including seabass, bream, and salmon. Thailand’s Kasetsart University recently found distinct benefits for shrimp, saying FeedKind promotes strong, healthy growth, while also helping activate shrimp’s immune response to Vibrio, the causative agent of Early Mortality Syndrome.
More capacity
Calysta’s protein platform is also approved for use in livestock feeds and pet food.
The joint venture partners are now focusing on bringing forward more capacity to address the Asian market.
According to Calysseo, FeedKind will help to reduce pressure on wild fisheries. If used instead of conventional sources of protein, 100,000 tonnes of FeedKind could mean that between approximately 420,000-450,000 tonnes of wild caught fish could be saved. Used instead of vegetable proteins, the same quantity of FeedKind could free up as much as 535 km² (206 square miles) of land and would save 9 billion litres of water.