
Prefab RAS installed at Norwegian smolt facility
Tank comes with integrated filters as part of the package
A first-of-its-kind prefabricated recirculating aquaculture system (RAS) has been delivered and installed at a smolt facility operated by salmon farmer Bremnes Seashore in Norway.
The OptiRAS module is a complete unit with an aluminium tank and integrated biofilter and drum filter and will be used for growing smolts. It was designed by Norwegian company SeaRAS, a specialist in aquaculture water management, and built at the Leirvik shipyard.
SeaRAS general manager Eldar Lien sums up the technology as compact, efficient, and cost-effective.
“The system combines water treatment technology in a new way and comes as a complete system ready for easy installation. We believe there is a lot of innovative technology out there, including high capacity to degas and clean through our own solution, real-time monitoring of water quality, and presentation and analysis of water and operational data through our software,” he told LandbasedAQ, a sister site of Fish Farming Expert.
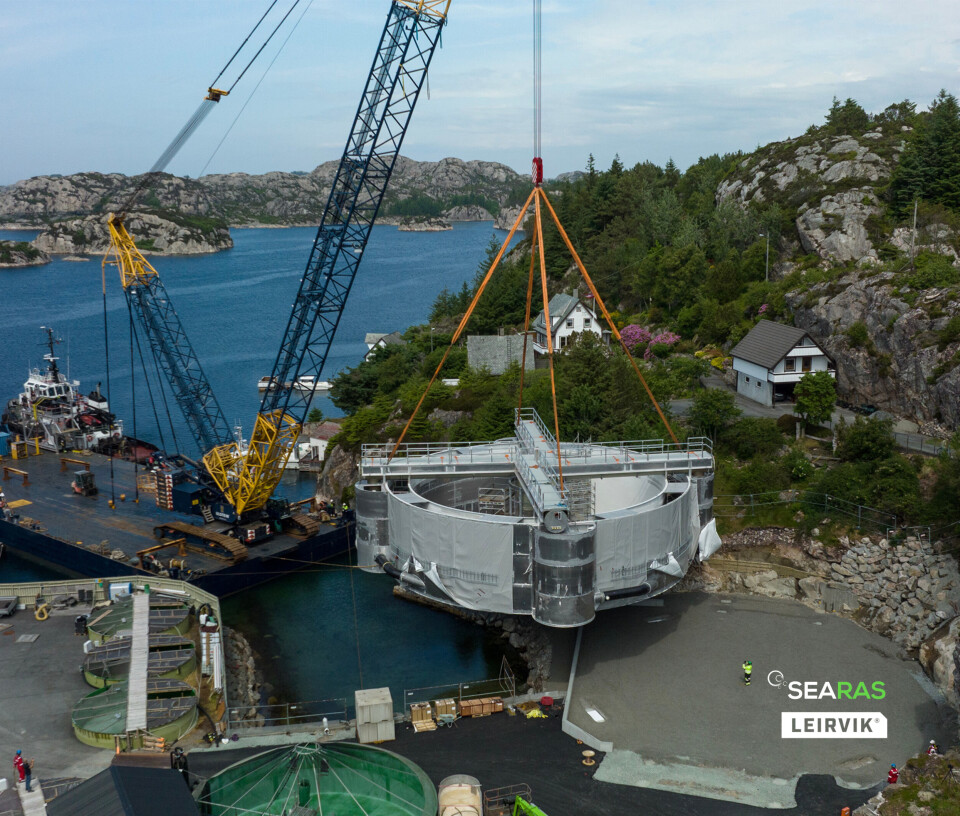
Lien noted that the solution represents a new way to solve the challenge of water treatment in RAS, while at the same time representing an entirely new model for the delivery of complex RAS.
“Most of the facilities being built along the coast today have a number of challenges. It costs a lot, takes a long time, and they are inflexible to adapting to new technologies. There are often large concrete projects with embedded pipes that are difficult to update. It is not particularly future oriented and incurs great cost when it has to be removed. It is not ecological either,” said Lien.
“This is a facility that can be moved, then relocated and sold, and therefore has great residual value. It will also be possible to finance it through leasing. It opens up a whole new way of doing fish farming.”
This is a facility that can be moved, then relocated and sold, and therefore has great residual value. It will also be possible to finance it through leasing. It opens up a whole new way of doing fish farming.
SeaRAS general manager
Eldar Lien
Lien said that the company hopes to verify the results when the prefab RAS at Bremnes Seashore’s Skålevik site in Bømlo, south of Bergen, starts operating in September. So far, the team has built several scale models to demonstrate the technology, where, among other things, power consumption has yielded impressive figures.
2kWh per kilo
“We have already demonstrated the energy consumption, and we see that we can get below 2 kWh per kilogram of fish produced. That is a quarter of what is currently used. That alone should be interesting for the industry,” Lien said.
“If you use 10 kWh or 8 kWh per kilo of fish produced, and you have someone else managing it with 2 kWh, you are giving yourself a big handicap. We see that, in theory, it is possible to go down to 1 kWh, depending on the number of additional functions that are included in the calculation. It will be a very exciting autumn when we see how we manage to document all the things we want to do.”
This first OptiRAS module has a diameter of 22 metres and a height of 6 m, and the module has a total volume of 2,100 m³, giving a capacity of 85 tonnes of salmon. Leirvik’s head of aquaculture, Arne Ottesen, has been involved in the first installation and is pleased with the work carried out.
An exciting push
“It has been an exciting push for us to have our own product for the first time, together with SeaRAS. It is the SeaRAS technology that is used, but together we have been responsible for the design of vessels and the integration of all equipment to be used on both vessels and platforms. It will be Bremnes who will operate it at the beginning of September,” explained Ottesen.
“We produce most of it in our shipyard, so we transport the entire vessel and equipment platforms and install everything in one day. In the future, we will do even more assembly in the shipyard and the connection work will be even shorter. Our objective is to have high standards at the same time that we can reduce costs and time.”
Ottesen claimed that the system can be produced and installed in at least 30% less time than current RAS. He is now excited about the results and a longer collaboration with SeaRAS.
“We have a lot of faith in the product and the plan now is that we will continue to collaborate with SeaRAS and provide facilities of this type to more companies,” he said.
“There are many interested in the products and the solution, but what most of them have in common is that they want to see it in use, and see the experience and see the results before daring to go ahead and invest. That is the whole purpose of the pilot that has now started.”
Watch a short video of the OptoRAS module's construction and delivery here.