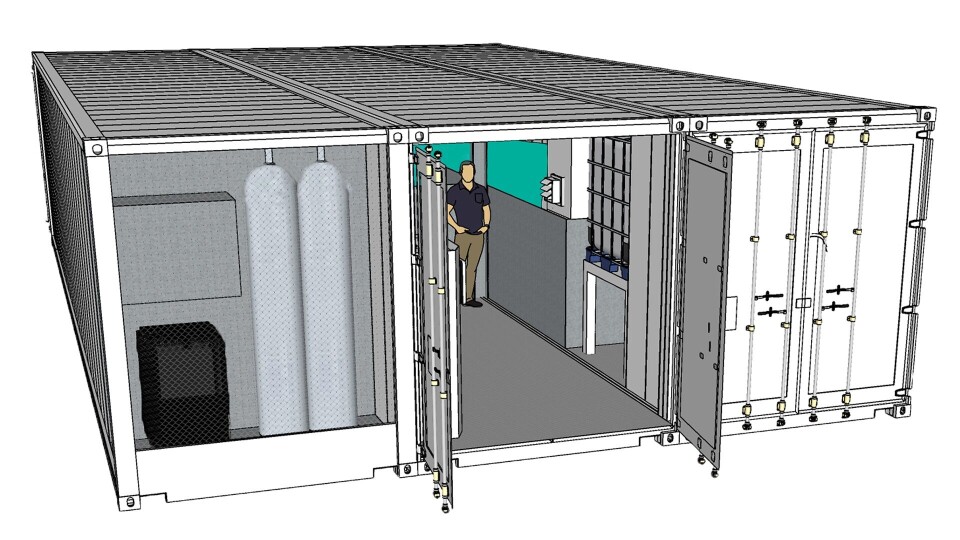
Thinking INSIDE the box: the fish farm in ship containers
A university spin-out company is offering what could be the ultimate in aquaculture convenience – an automated recirculating aquaculture system (RAS) fish farm housed in three interconnected shipping containers.
The compact RAS from SEAWATER Cubes is aimed at both freshwater fish farmers wishing to expand into marine fish and land farmers looking to diversify. Restaurateurs and businesses such as sushi chains looking for ultra-fresh fish are other potential customers.
The Cube is designed to bring marine farming inland, allowing farmers to offer sustainable fish grown locally. It takes up just 100 square metres of floor space and because it uses a domestic tap water supply it can be sited almost anywhere. It can produce seven tonnes of fish annually.
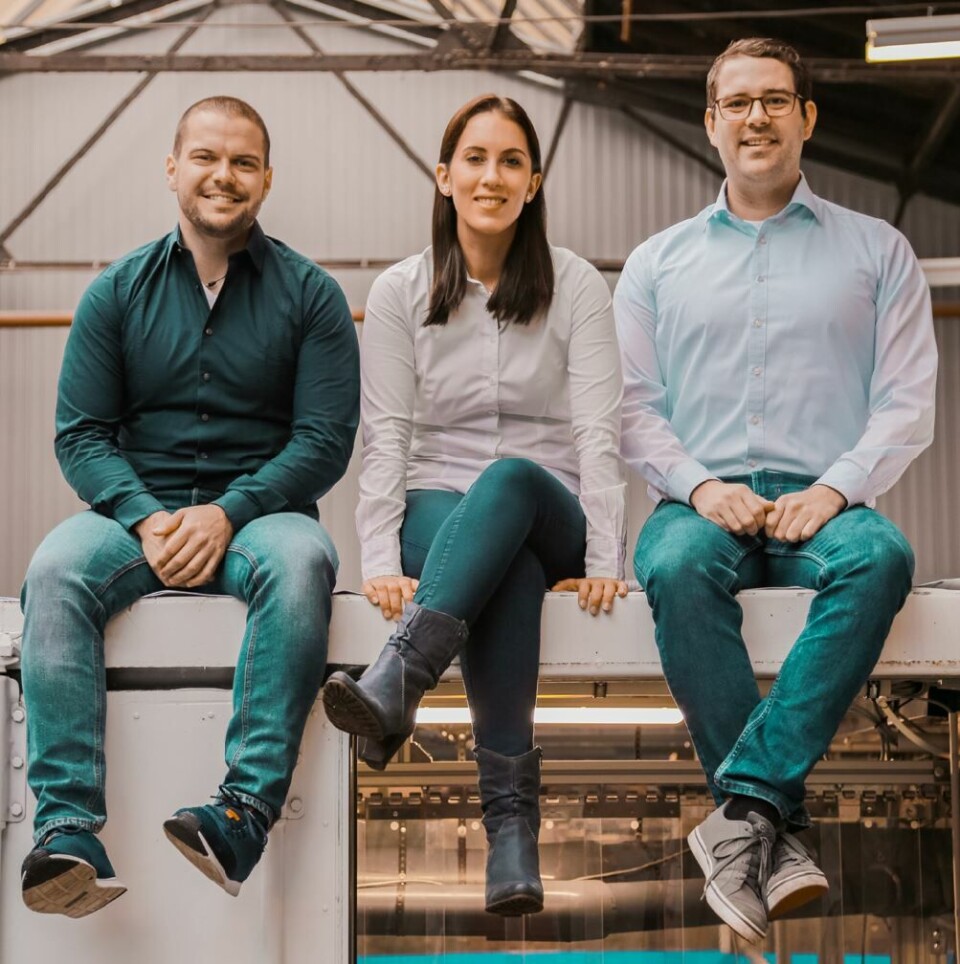
Seabass
The Cube is the brainchild of SEAWATER’s managing partners Carolin Ackermann, Christian Steinbach and Kai Wagner, former students at the University of Applied Sciences (htw saar) in Saarbrucken, Germany who were employed in the university’s aquaculture laboratory after gaining their degrees.
After acquiring substantial knowledge about fish farming in general and about highly technical, closed RAS in particular, they decided to start their own company.
Help by funding from the German government’s EXIST – Transfer of Research programme, they have been growing seabass in their prototype Cube since October 2018.
The fish take between eight and 12 months to reach market size of 400-500g.
Three year classes
Ackermann told Fish Farming Expert: “In the farm itself we have three different year classes. They are all in one tank but are separated by nets. You need one year to get the first fish and then you have fish ready every four months. You put fingerlings in every four months.”
The next cycle will use gilthead bream, which require the same conditions as seabass.
The entrepreneurs also plan to adjust the Cube for the farming of yellowtail kingfish, black tiger prawn, red snapper and Malabar grouper.
The Cube performs all control and monitoring tasks and all Cubes will be linked to the company’s headquarters via the internet. According to its creators, this enables virtually unattended plant operation and reduces the workload for the plant operator to an average of 1.5 hours per day.
Water is filtered three times an hour, and less than 1% of process water needs to be replaced daily.
The cost of one Cube is €250,000 (£215,000). The company will also provide a processing unit in a fourth container. This costs an extra €50,000 but has the capacity to handle production from up to five Cubes.
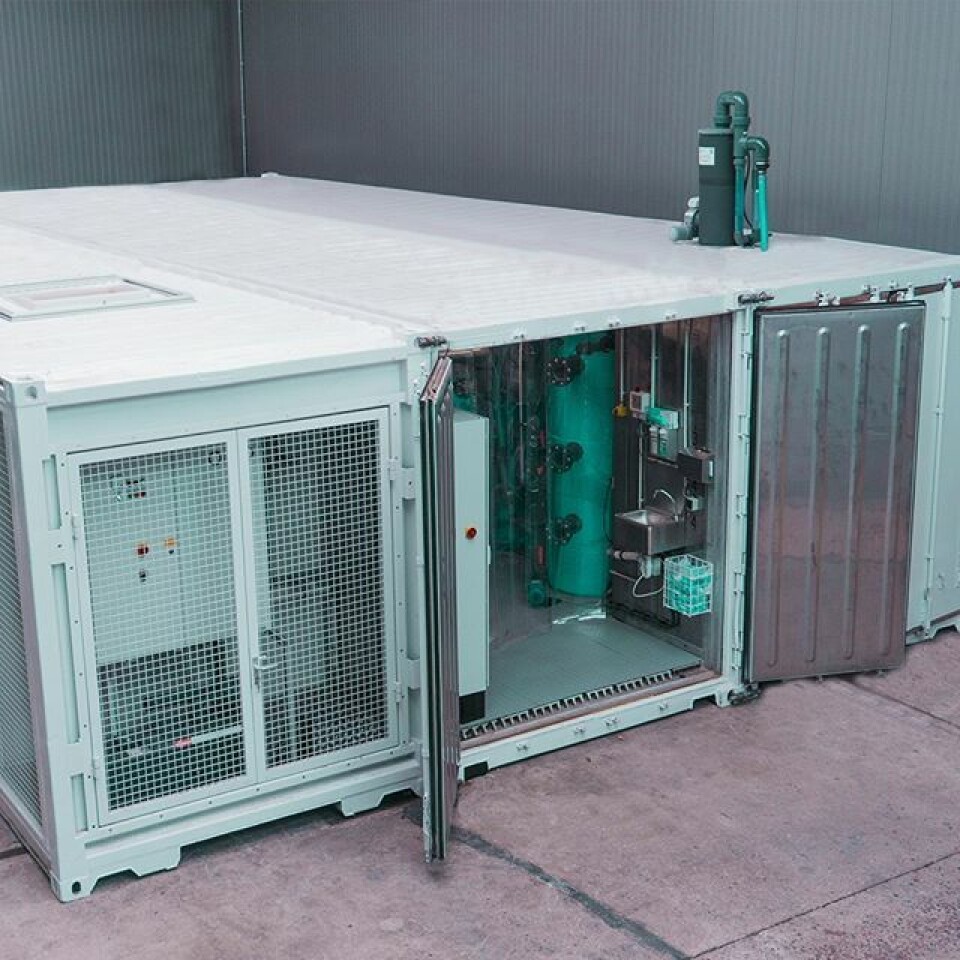
Fingerlings and feed
SEAWATER Cubes will also provide fingerlings, organic feed, a special mix of minerals to give the water the same make-up as seawater, and everything else needed for production, as part of a separate package.
“Our goal is to offer an all-inclusive service,” said Ackermann.
“Our main market is fish farmers who already have freshwater production and land farmers who do not earn enough money with cows, eggs, etc.”
German market first
She said the company had talked to some German restaurants about growing their own fish, but they were more interested in buying the fish from a farmer.
“But we have only talked to smaller restaurants. We have not yet talked to larger chains or sushi chains.”
“We plan to sell the first Cubes next year and we are talking with prospective buyers in Germany. We plan to sell five or six next year,” added Ackermann, who said the Cube had attracted a lot of interest from abroad, including Israel and Saudi Arabia.
“There is a huge interest in the concept but in the first year we will concentrate on Germany.”
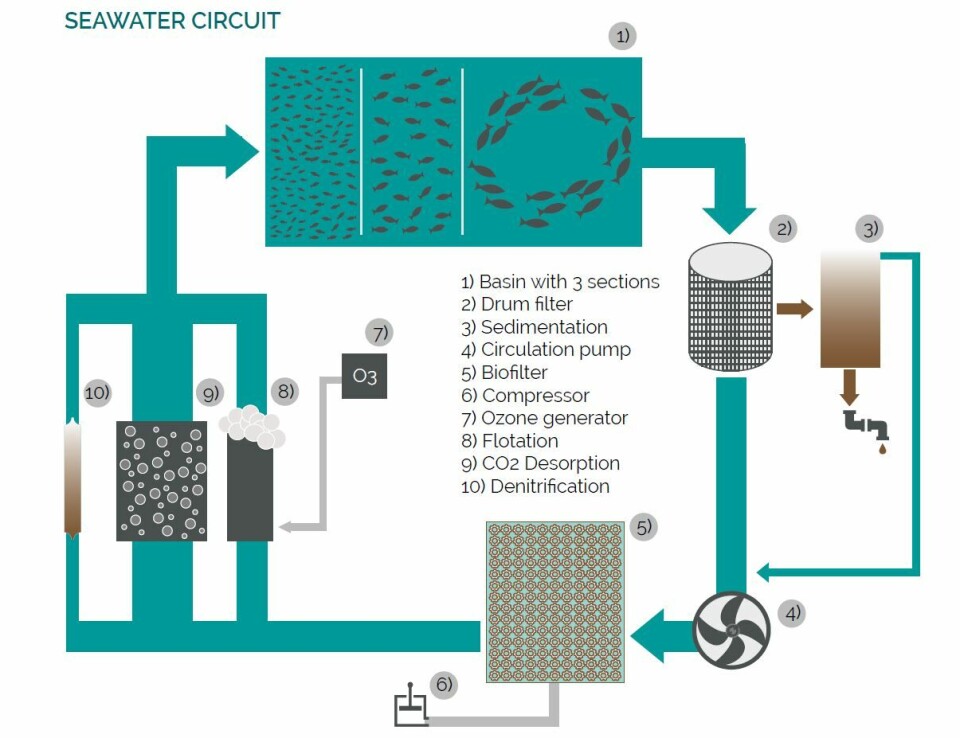
100 litres of sludge
Ackermann said the Cube produced 100 litres of sludge per day. This had relatively little salt in it, so land farmers could mix it with their animal manure, or it could be disposed of in the same way as other sewage.
“In the future we hope to use aquaponics to get rid of sludge,” she explained.
Water replacement for the RAS is 500 litres per day.
55 fish per day
The capacity of the Cube is deliberately low – it works out at a continuous year-round supply of around 55 fish per day once harvesting begins – and is based on the marketing reality that SEAWATER Cube’s founders experienced at their university’s fish farm.
“The farm could produce up to 600 tonnes per year, but they couldn’t grow sales fast enough,” said Ackermann. “They were only able to sell 100 tonnes of fish.
“The Cube is made for the direct sales of fish, either to the end consumer or to restaurants. It is only 50 or so fish per day, so you have time to build up your sales.”
SEAWATER Cubes will offer marketing and sales support, helping new farmers find sales opportunities tailored to their individual needs.