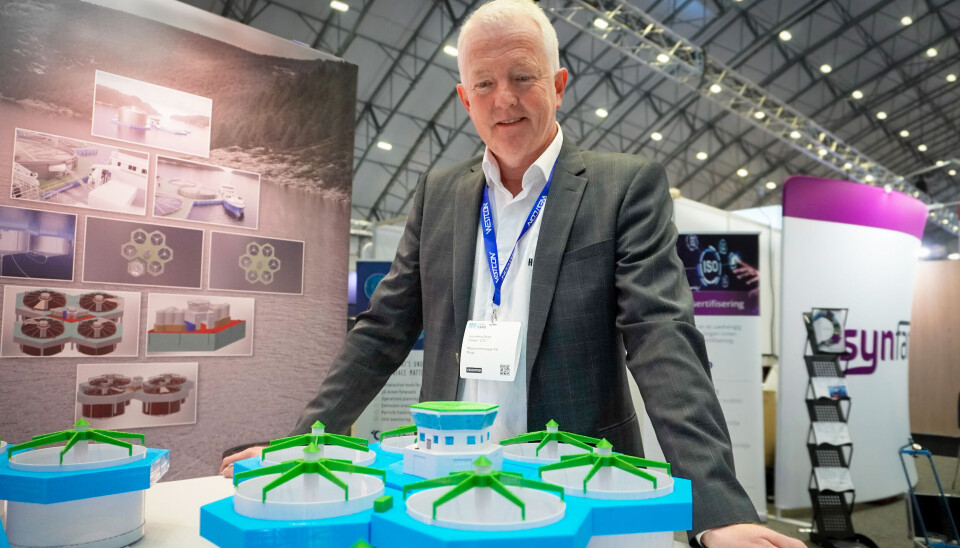
The farm with six appeal
With closed steel cages, Westcon Hexacage is approaching a critical step in development in what it believes can help change the farming industry for the better. Soon the first contract will be signed.
A Norwegian company that has designed an environmentally friendly, all-in-one floating closed containment system for salmon farming is close to signing its first contract, it says.
Westcon’s Hexacage is a unit that consists of closed steel cages that surround a service cell. Each cage operates in isolation with its own machine rooms, filters, and pumps, and the service cell houses common infrastructure. It contains, among other things, various engine rooms, feed storage, emergency generators, and storage capacity for sludge.
The core of the concept is that the fish get peace. No lice treatment, no handling, no pumping, but stable access to plenty of good water, is Westcon’s ambition. Another key element the company highlights is that a flexible water intake system is used to retrieve water from a temperature-friendly depth. The system is also modular, so the farmer can choose whether he wants one, two, three, four-five or six cages, connected to the service cell.
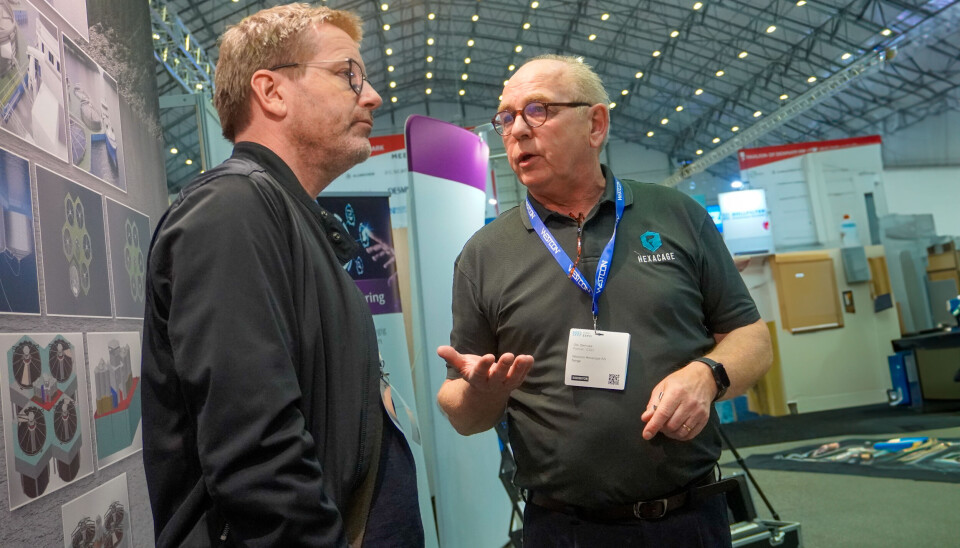
Cutting steel soon
During HavExpo in Bergen, staff from Fish Farming Expert’s Norwegian sister site, Kyst.no, met Ole Bennæs, partner in Westcon Hexacage and Arne Matre, general manager of the company.
The two are convinced that the salmon sector’s future is dependent on biology.
“We believe that if you don’t fix the fish health part, and animal welfare, then it matters very little how good you are at the rest. It will only become more and more important,” they emphasise.
What is the next step for you now?
“Now we have finished all structure and strength calculations and all dimensioning. Hopefully we will have a signature (for the first order) before the holidays on the pilot, and then we will build the first cage. The hope is therefore that we will start up and cut steel relatively quickly,” Bennæs and Matre say.
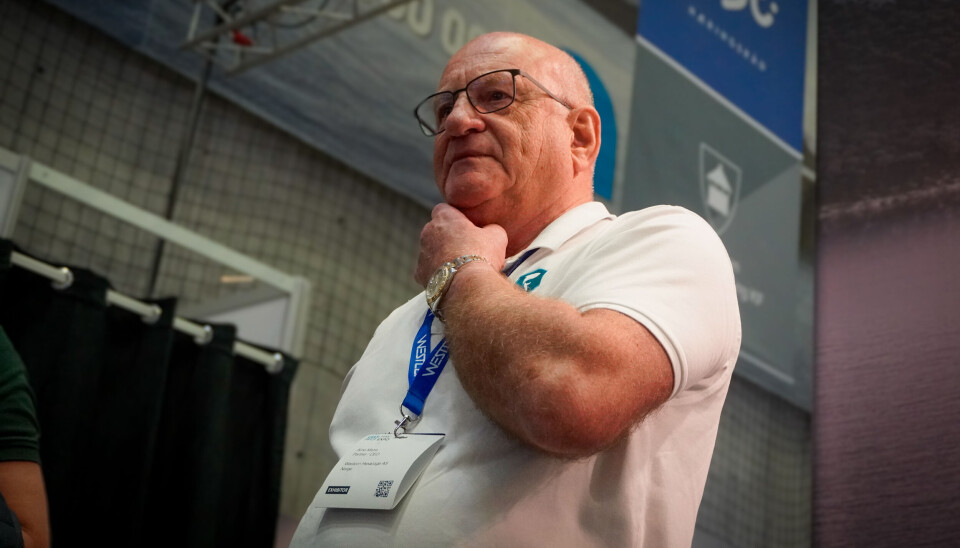
Knocking on doors
The company has tested the facility on a small scale at engineering institution Sintef in Trondheim, where a 1:30 scale model was built.
“The design criterion is HS 4.3, and it works brilliantly,” says Matre.
He adds that they have spoken and had communication with five or six farmers, who are very involved in giving them advice, but Westcon has not yet begun to push its product hard.
“But if we can now flag a signature before the holidays, then we can start knocking on doors with a full-scale facility.”
Westcon believes that getting closed facilities at sea is not a technological problem, but a regulatory problem.
“We have a government apparatus that is not always at home. And it is not at home even when it is present. They are on another planet, and therein lies the problem,” Bennæs believes.
Confirmation from biologists
How do you view the competition from others?
“There are some concepts out there, but I don’t think I’ve seen any that are both flexible and dimensioned to operate on such an industrial level. The working platform we are presenting, it is much like it is on land,” say the two.
Another advantage they highlight is that material they have chosen is steel. This means that they can cut and weld and make changes without it challenging the structural strength of the plant, which would be more challenging to achieve in, for example, polyethylene.
Matre says they have now had all structures verified, and he is clear that they are now ready to start cutting steel.
“We have also received confirmation from biologists that the way we think at full scale has been tested in scaled-down versions by both the University of Bergen and the Institute of Marine Research. They tell us that there is no reason why we should not get the same positive biological results that they have seen in smaller trials.”
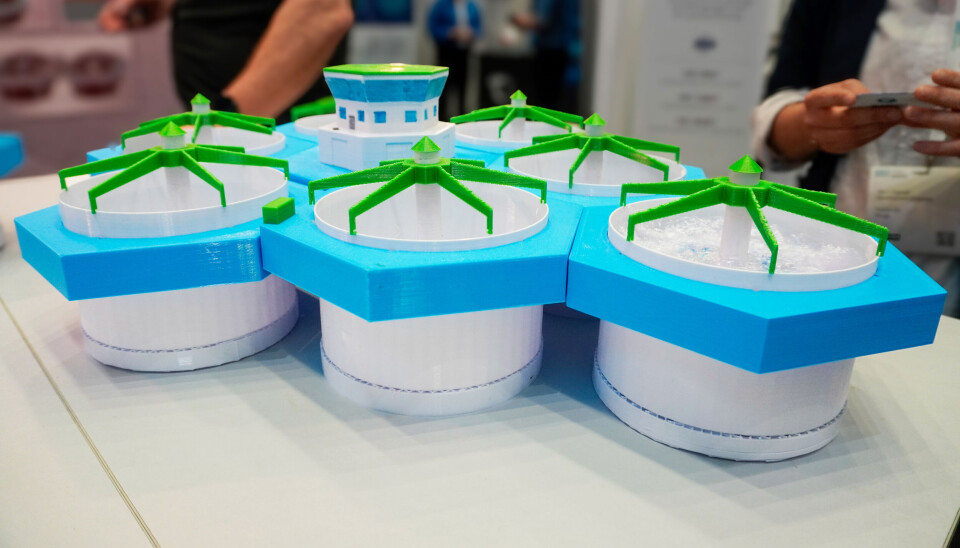
Plenty of lice-free water
The company has simulated models where they take the fish from 100 grams up to harvest in the closed facility, but the company it is now close to signing a deal with has said that it will initially take the fish up to 1.2 kilos in the facility, and use it as a pure production of post smolt.
Matre explains that in Westcon’s facility the focus is on the fish, and they must have plenty of lice-free water.
“The principle is that all incoming water is filtered for lice and larvae. A cylindrical cage shape makes it possible to get a homogeneous water flow in the cage itself, and we have full control over setting the current speed. It must be adapted to the size of the fish at all times. Physics allows us to move fish, either to another cage or to a boat, using gravity, without the use of pumps. The goal must be that the fish can live through an entire life cycle without handling or being pumped,” explains Matre.
He believes it is also important to think about the environment in which the cages will be located.
“There are too many injuries and accidents, and demands will be made for a lower number of accidents. We have taken the working conditions for the farmers to a completely different level than is common in today’s cages.”
The opportunity to collect data and be able to use the results to improve operations, he believes, will also be raised to the same level as on land, but with operating costs far below land-based costs.
The first agreement is expected to be signed shortly, with a farming company looking to operate a full-scale pilot edition.
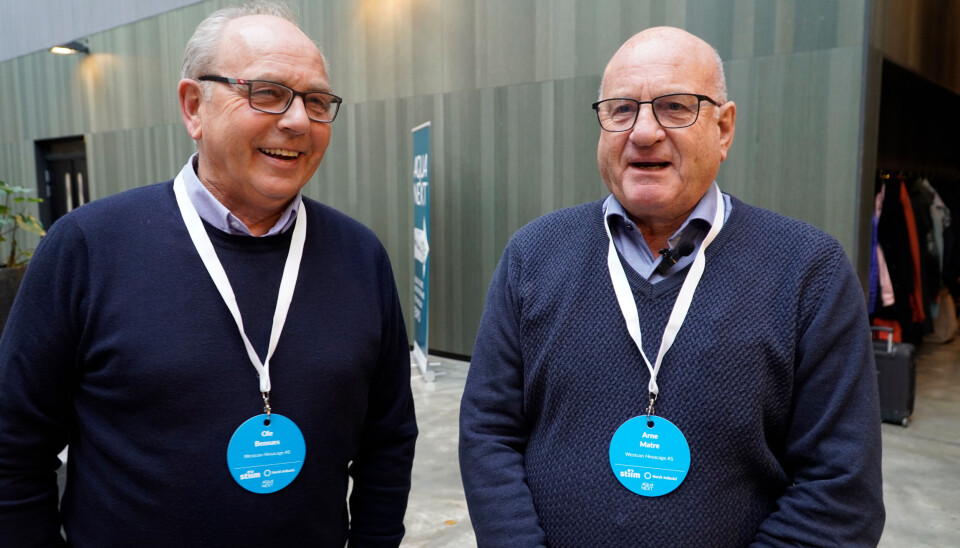