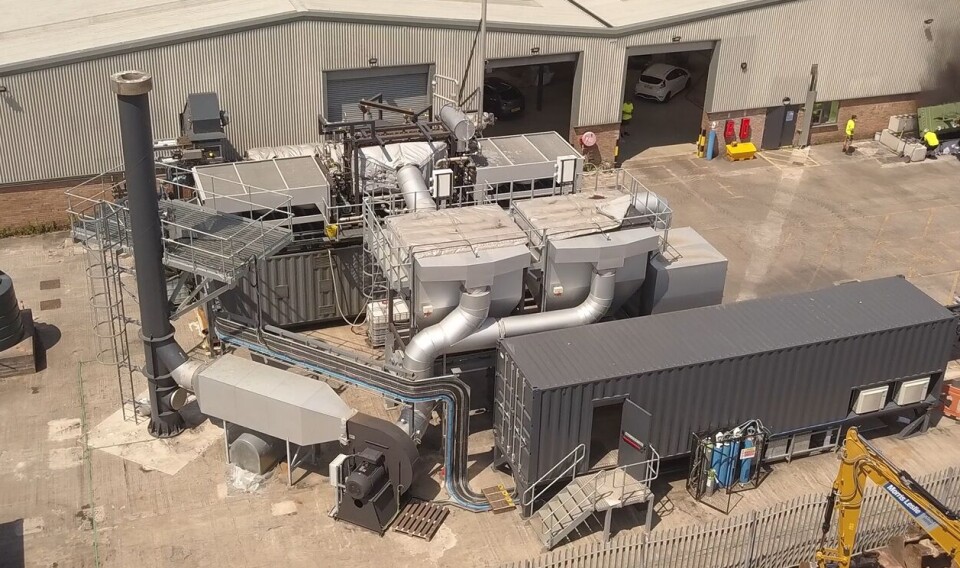
‘This is how farming can become carbon negative’
Through pyrolysis, you can get a product that deposits carbon, takes care of phosphorus, and becomes a valuable soil improvement product, says Stuart Caley of UK-based PyroCore
PyroCore is the company that develops the pyrolysis technology that aquaculture sludge handling systems supplier Blue Ocean Technology offers as the end module. Primarily, Blue Ocean Technology is concerned with extracting, dewatering and drying sludge but can now also offer an extra step, which can prove to be very valuable for fish farmers.
Blue Ocean Technology’s managing director, Hans Runshaug, says the company experienced great interest in the method during fish farming trade show Aqua Nor in August.
“A lot of people stopped by our stand to hear about this,” he tells Fish Farming Expert's sister site, Landbased AQ. “We actually ran out of brochures, and that must be the first time in my long Aqua Nor ‘career’.”
Watch the sludge pyrolysis process
(Explained in English)
And on that stand the company had pyrolysis expert Stuart Caley, from PyroCore, based in Avonmouth, Bristol in the UK.
Combustion process
“Pyrolysis is a combustion process that occurs by first forming an oxygen-free gas called syngas (synthetic gas), which is then burned. What you get out of it is a lot of heat - which can be used for everything from direct heating to the production of electricity - and we are left with a residual product that consists of carbon in addition to ash,” Caley explains.
He says that almost anything that is carbon-based can be put into the process.
“We can process everything from broken and worn out wind turbine blades, to household waste, sewage and therefore sludge from fish farming,” he says.
Runshaug is fascinated by the possibilities.
“With this technology, we can get new products out of fish sludge and really contribute to creating a circular economy,” he says.
Self-fuelling process
Caley explains that in the process some of the carbon is converted into methane (syngas). This is sent back into the process and used to keep the heating constant.
“But you are still left with around 35-40% of the carbon and a lot of the nutrients. This becomes a ‘super fertiliser’ if you mix it with compost, for example,” he says.
He points out that if sludge from a land-based fish farm or hatchery is used directly as fertiliser, all the carbon will be released relatively quickly.
“In the pyrolysis process, you lock in the nutrients, so that the plant roots have to get the nutrients themselves instead,” he says.
Caley adds that pyrolysis itself is not at all a modern invention.
“Burning wood without access to oxygen has been done for thousands of years,” he says. “One can, for example, find 2,000-year-old biochar in the Amazon. Here, this has been used as soil improvement, long before the Europeans arrived. The solution is old, but we have made it very effective. And experiments have shown that biochar makes the soil extremely productive.”
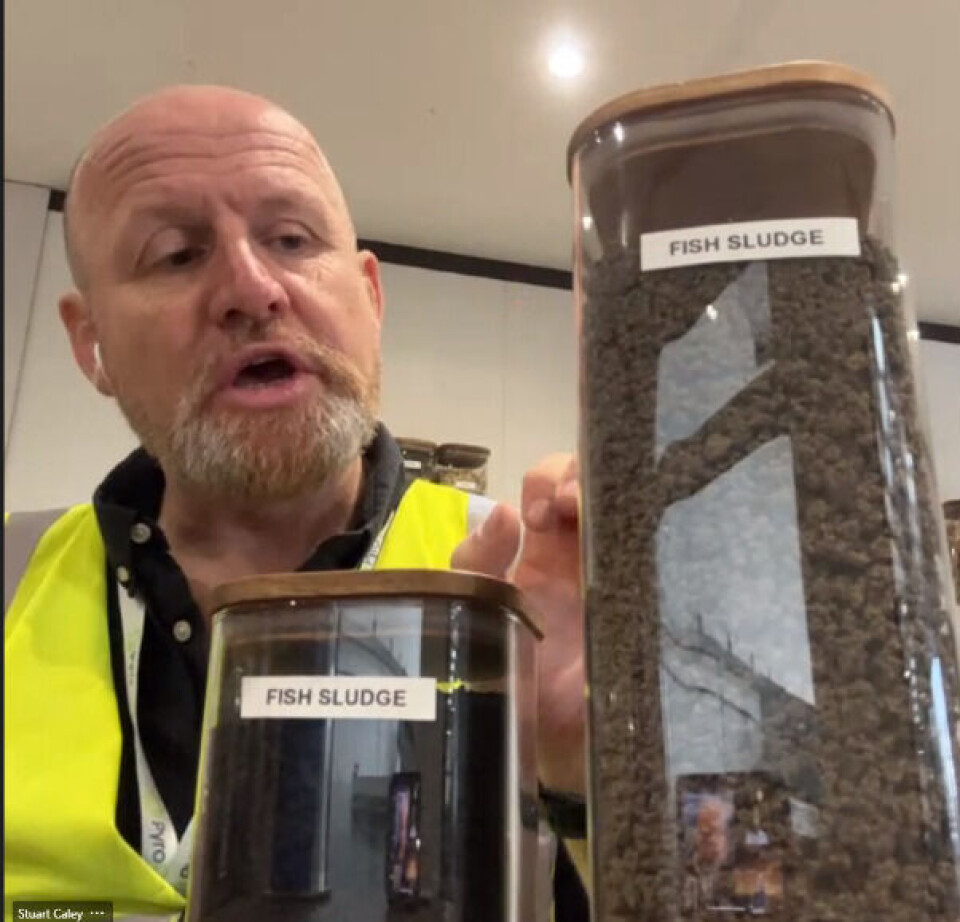
A valuable product
“The great thing is that we not only remove a problem that sludge can represent, but we turn it into a valuable product,” adds Runshaug.
He says that much of the feedback from Aqua Nor was that people do not know about this.
“When the authorities talk about carbon capture, this is never talked about. Only about storing CO2 under the seabed, which is both very expensive and uncertain. What if an earthquake causes everything to be released again,” he asks.
Runshaug says pyrolysis is the only method to not only capture the carbon, but also put it to use.
“This is a safe way of handling it while at the same time having a positive environmental impact,” he says.
Runshaug also points to the residual waste from biogas plants, where pyrolysis is essential to solving this waste problem as well.