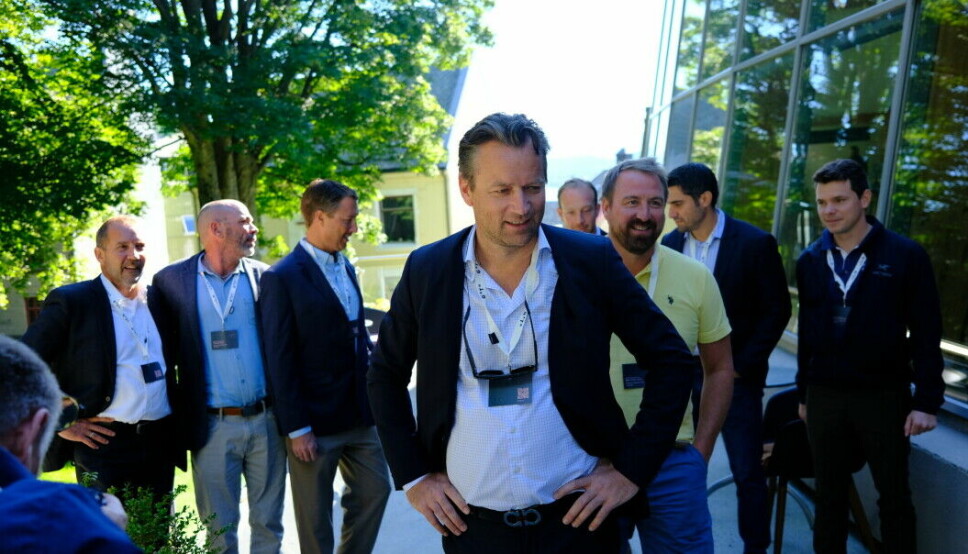
We’ve learned from our mistakes
Problems with the first phase of Atlantic Sapphire’s planned 220,000-tonne on-land salmon farm in Florida have led to a different and better approach for phase 2, says boss Johan Andreassen
Andreassen was sparking at the GATH (Global Aquaculture Tech Hub) conference taking place this week in Ålesund, Norway.
Speaking to an international audience of fish farming suppliers, the Atlantic Sapphire co-founder said that everything had not gone according to plan when the first fish tanks with associated recirculating aquaculture systems (RAS) were being built at the company’s Bluehouse facility in Homestead, Miami.
“A lot went wrong when we built out phase 1, and the cost was roughly double what we had planned. Eventually we got to production, and we have now – since each tank is strictly speaking a separate RAS plant – managed what corresponds to 20 years of operation of a single independent RAS system without mortality events,” said Andreassen.
Role of RAS supplier
One of the things that has also changed is the view of what role the RAS supplier has in what is often simply called a RAS facility.
“Many believe that RAS is the major cost of a land-based facility. It is not! The RAS plant itself may only account for 15% of capital expenditure when a new plant is to be built. We also thought that the RAS provider could solve any problems that arose. That’s not true either,” he said.
A RAS plant is actually a water and sewage plant with fish in it. That’s why we went to the company Hazen and Sawyer
Johan Andressean
Before starting phase 2, the company therefore spent a lot of time to find what was, for them, the right way to proceed.
“We thought, what is most similar to a RAS plant of existing industry? Yes, a water and sewage system. A RAS plant is actually a water and sewage plant with fish in it. That’s why we went to the company Hazen and Sawyer, which we believe are the leaders in the USA in everything to do with water and sewage engineering.”
Tasks farmed out
The choice meant that instead of Atlantic Sapphire employees working separately on permits, water infrastructure, architecture, engineering calculations, ventilation systems, etc., as they did in phase 1, Hazen now manages all of this.
“We have also chosen to work with Wharton-Smith, which is a large developer of water and sewage systems in the USA, which has been doing this for several decades,” said Andressean.
But even though Atlantic Sapphire has now hired these companies to manage planning and development, Andreassen offered reassurance to Norwegian companies who now possibly fear that they will not be allowed to take part in supplying equipment for the development.
Norwegian equipment
“To those who are worried that there should not be Norwegian equipment in the facility, I can say; it won’t happen. In phase 2 alone, we have so far purchased equipment for NOK 3-400 million that we have ordered from Norway. We have, for example, bought the fish handling system from MMC, where in principle we have moved the wellboat technology onshore,” said Andreassen.
To emphasise the point, he said that he had brought people from the organisation to Norway to learn.
“We are here with eight people from the USA, to look at the supplier industry and the farming industry in general.
“I am still equally impressed by seeing what must be salmon’s Silicon Valley, the Ålesund region,” he said.
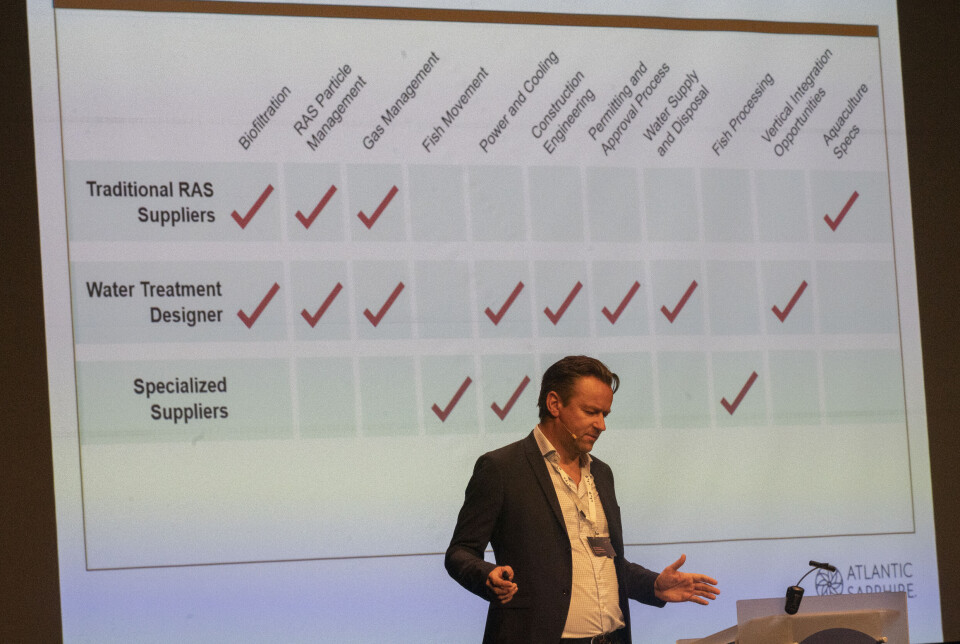