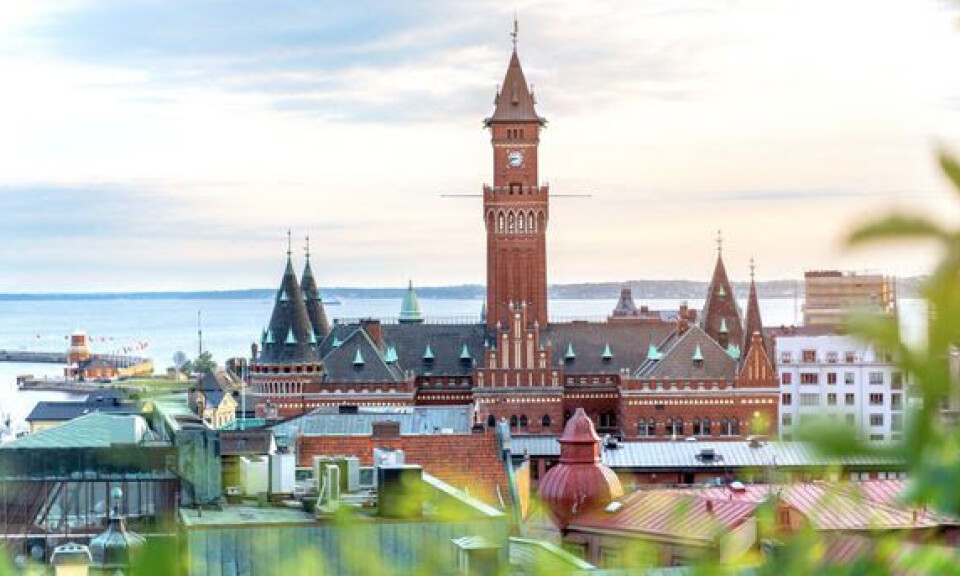
Recycling company will recover phosphorous from salmon sludge
Ragn-Sells commits to new factory in southern Sweden
A plant that can recover phosphorous from both sewage and fish farm sludge is to be built by Sweden-based recycling company Ragn-Sells.
The company said more than 11,000 tonnes of phosphorus – an important resource that currently has be mined and is mostly imported from outside Europe - are wasted by the Norwegian aquaculture industry each year.
The new plant in Helsingborg, a port city on the shore of the Öresund strait separating Sweden and Denmark, is based on the Ash2Phos technology of Ragn-Sells Group’s innovation company EasyMining. Through the process, more than 90% of the phosphorus in the ash from incinerated sludge can be recovered.
“If we are serious about creating a sustainable society, we must use the resources we already have, over and over again,” said Anders Kihl, research and development director at Ragn-Sells Group. “Thanks to our owners' decision to invest, we can finally begin the installation of our Ash2Phos plant in Helsingborg. This is an important step towards enabling sustainable phosphorus recycling both in Sweden and in Europe.”
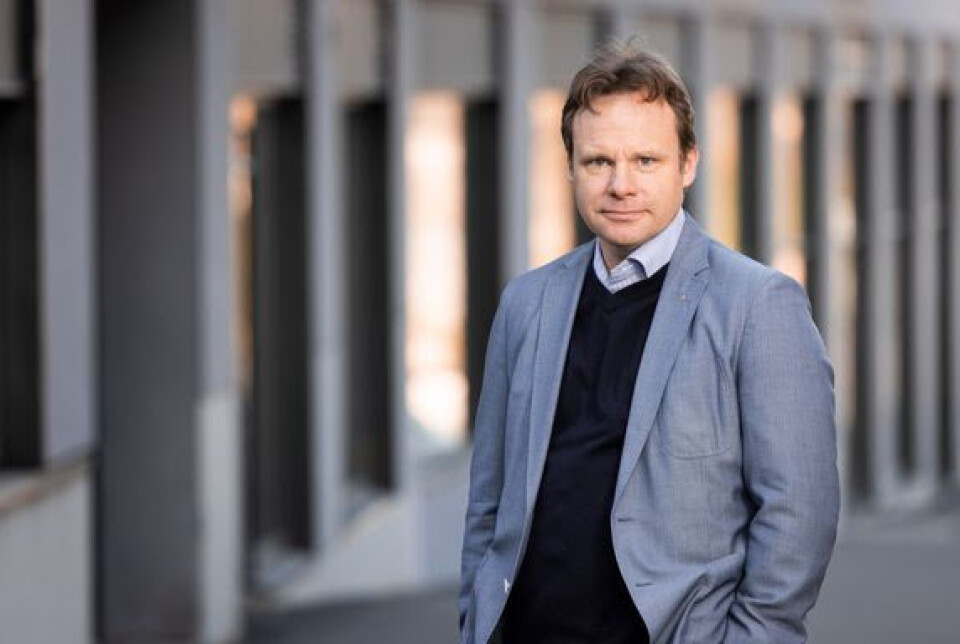
15,000 tonnes per year
Phosphorous is included in mineral fertilisers and animal feed and is necessary for agricultural food production. At the same time, demand is increasing to enable transition to a lower carbon economy, because phosphorus can be used in the production of new batteries.
The Ash2Phos plant in Helsingborg will be able to handle 30,000 tonnes of sludge ash per year, which corresponds to the production of 15,000 tonnes of phosphorus in the form of calcium phosphate per year.
Before the Ash2Phos process begins, a chemical is added to wastewater to separate the phosphorous and bind it to the sludge. The sludge is then incinerated to remove contaminants and reduce volume.
The Ash2Phos uses more than 95% of the ash. The process starts with dissolving the ash in an acid and filtering the silicate fraction – a sand - which is washed and can be used as a cement replacement in concrete. The solution portion contains the phosphorous, iron, aluminium, and heavy metals, which can all be separated.
A chemical manufacturer, Kemira, will reuse both the iron and aluminium, which provides a further step towards circular wastewater management.
Second factory
The Ash2Phos factory in Helsingborg will be its second factory for phosphorus recovery in Europe. The first factory, located in Schkopau in northern Germany, is under construction and is planned to be operational by 2027. It has the same capacity as the Helsingborg plant.
Recovered phosphorus is chemically equivalent to virgin (mined) phosphorus, but contains fewer contaminants, such as heavy metals. This makes the use of recovered phosphorus safer in the food supply chain, said Ragn-Sells. Recovering phosphorous is also greener than mining.
“By recovering phosphorus from incinerated sewage sludge, we can reduce emissions by approximately 20,000 tonnes of CO₂ annually, while contributing to a safer food supply for Sweden and Europe. The plant also opens up more circular material flows in the future, which gives us hope for a more sustainable and resource-saving world,” said Kihl.