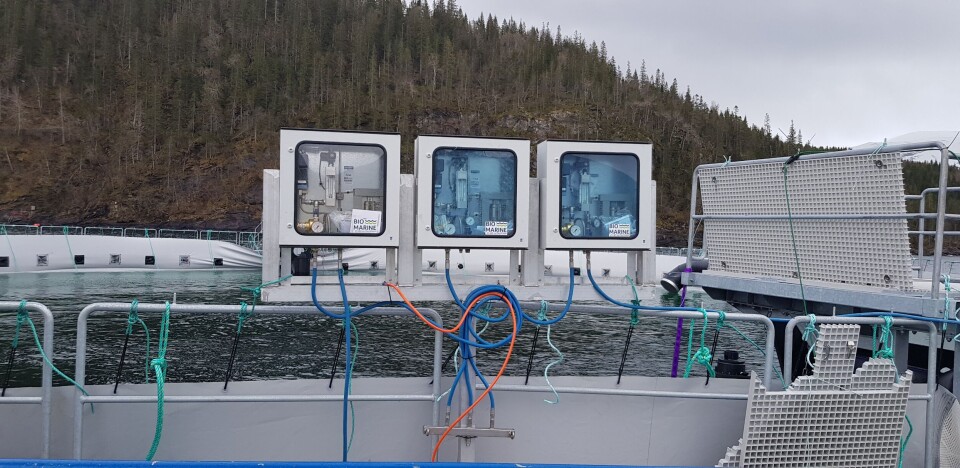
Closed cage farming ‘must rely on supplied oxygen’
Closed cages in the sea provide the ability to control the water environment and ensure optimal conditions for fish health and growth, and are beginning to be adopted in Norway, particularly for smolts.
But salmon farmers will not be able to rely on the natural level of oxygen in water to meet demand from the fish, whatever the rate of water exchange, an expert in the field has said.
Effective solutions for oxygen will be a decisive factor in the profitable operation of the cages, according to Asbjørn Bergheim, research manager for oxygen diffuser supplier Oxivision.
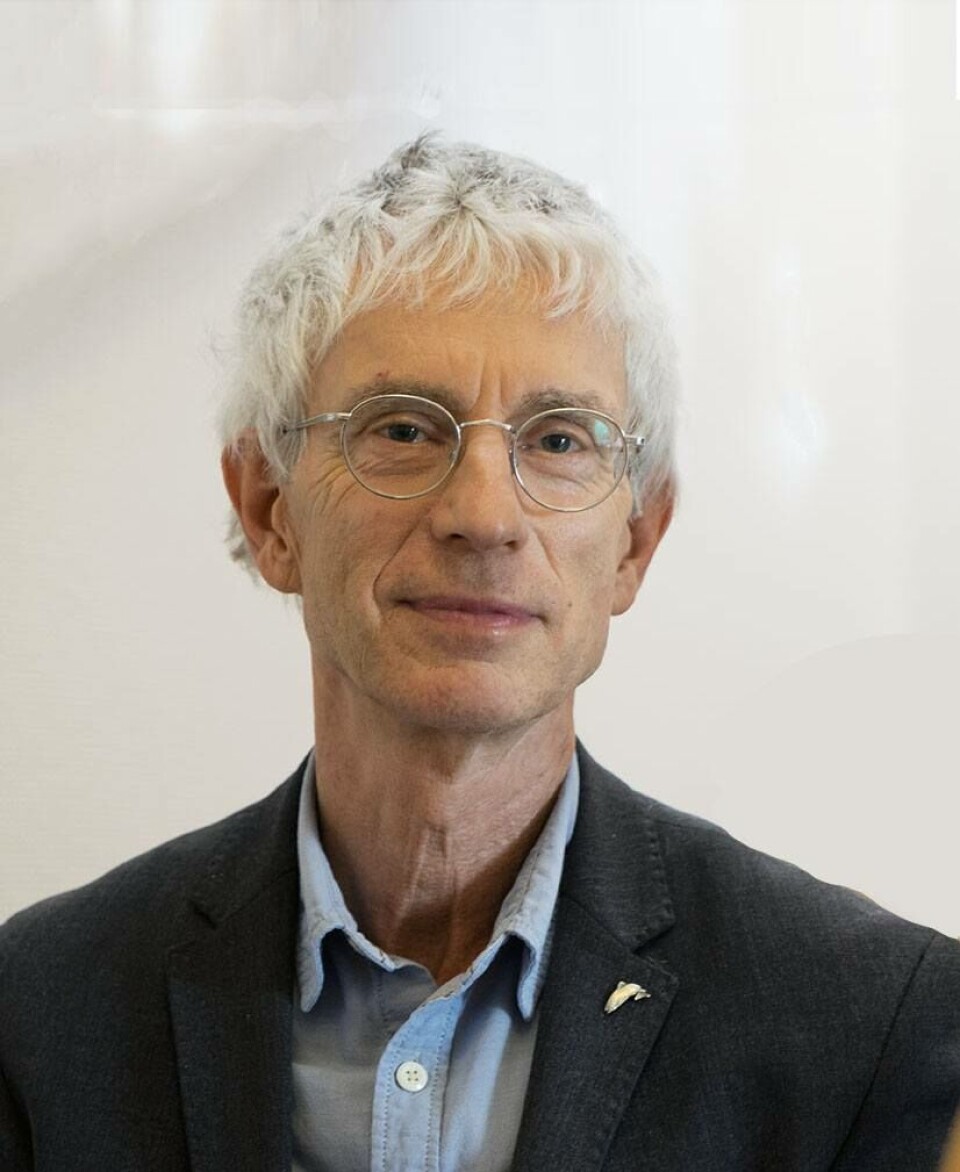
Higher fish density
Bergheim has written a series of articles for the magazine Norsk Fiskeoppdrett (Norwegian Fish Farming), a sister publication of Fish Farming Expert, the first of which looks at the oxygen needs in closed cages.
“Closed cages have a number of advantages compared to traditional open cage farming,” says Bergheim. “Closed systems eliminate or greatly reduce lice problems, increase safety against escaping fish and makes it possible to collect and utilise particulate waste.
“However, construction of closed systems requires larger investments, which however can be overcome by more efficient utilisation of the cage volume; first and foremost by maintaining higher fish density than in open cages.”
Diffuser network
He points out that in order to maintain high production and good fish welfare, in practice all oxygen consumed in closed cages must be added.
“All such operations make use of a system for oxygen dosage, often through a diffuser network placed inside the cage,” says the scientist.
“The water pumped from depth into the cage normally contains high oxygen levels, in the range 80 - 100% of saturation. For maximising the fish’s growth potential, oxygen levels in the cages should not be below 60 - 70% of saturation, at least, not for long periods at temperatures above 12 - 14°C.”
Carbon dioxide
The requirement for relatively high fish density in the cages cannot be compensated by pumping more water, stresses Bergheim, so the water exchange in relation to the fish biomass should be kept at a modest level.
“A normal water consumption in closed cages with normally high density of post-smolt and larger fish usually is around 0.2 - 0.4 l/kg/min (litres per kilo of fish per minute). At temperatures in the range 6 - 10°C, the fish then consume between 5 and 10 mg oxygen per litre of new water,” he says.
“In reality, it is the accumulation of carbon dioxide (CO₂) in the water which will determine the level of production. To avoid CO₂ levels above 10 mg/l, the water supply cannot be too low - a recommended lower limit is around 0.2 l/kg/min.”
Dosage control
He points out that experience indicates that oxygen consumption is around 300 - 400g per day per kg of fish produced.
“Assuming effective control of the oxygen dosage and utilisation throughout the production cycle, the approximate need for extra supply at the farm is around 0.5 kg oxygen per kg of fish produced.”
He gives an example where the oxygen demand in a closed cage of 5,000m³, with a density of 40 kg/m³ (i.e. 200 tonnes of fish) is about 500 kg at high water temperature, during summer - autumn.
Accurate measurement
“With such an oxygen demand, the efficiency of the oxygen diffuser system is an important factor for the profitability in closed cages,” says Bergheim. “This requires both high efficiency of the diffusers, optimal addition strategy and accurate measurement of the oxygen level in the water.”
Bergheim has been research manager for Norwegian company Oxyvision and its subsidiary Bio Marine since 2018.
He is a former senior researcher and adviser in aquaculture at Rogaland Research/IRIS 1985 - 2018, with water quality and environmental technology in aquaculture as expert fields. He has long experience in developing closed farming systems, including R&D for Akvafuture in Brønnøysund, Norway.