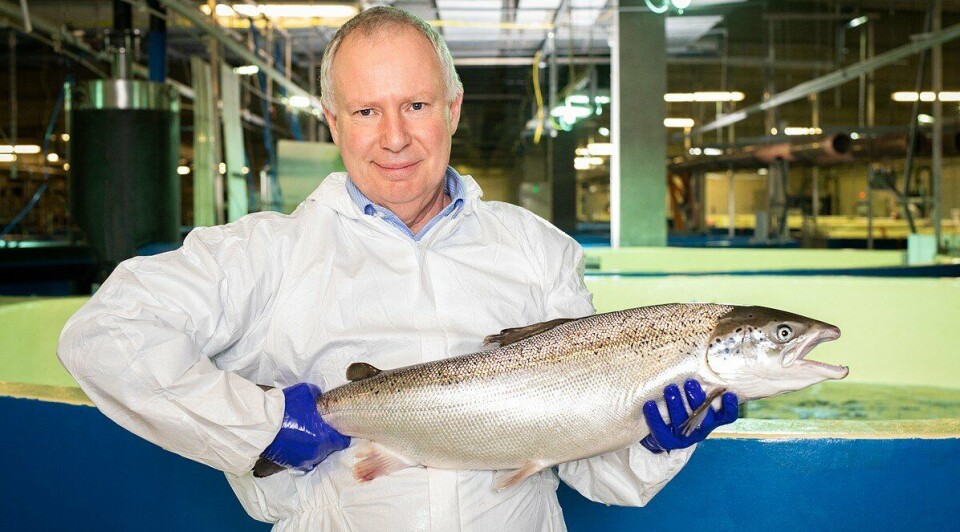
Can Pure Salmon change the game for RAS grow-out?
A recent study for Highlands and Islands Enterprise concluded that on-land salmon farms being built around the world posed no immediate threat to the Scottish industry’s expansion hopes. Pure Salmon’s plans may prompt a re-think.
The company, set up by investment management company 8F, intends to build enough recirculating aquaculture system (RAS) facilities to harvest 260,000 tonnes of Atlantic salmon annually.
And it plans to do it all within the next five or six years.
“This is the first time that anyone has done a proper global roll-out of large-scale RAS facilities,” says Martin Fothergill, a partner in 8F.
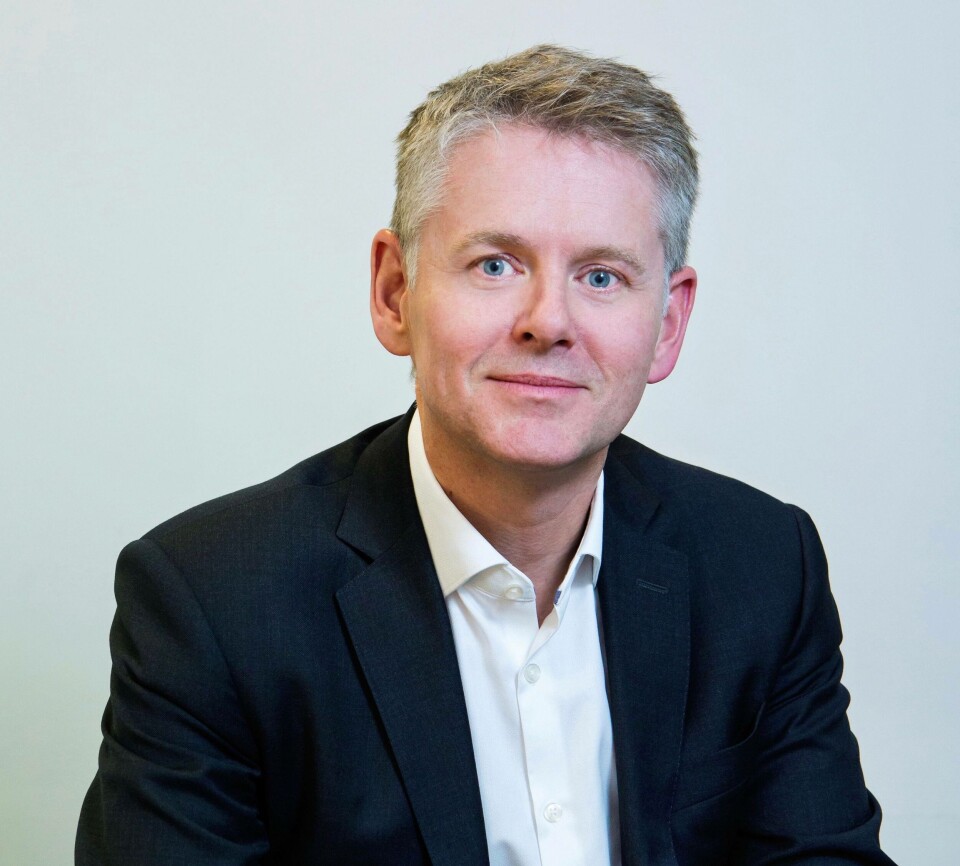
Time to industrialise
“All we’ve seen prior to this is people announcing individual facilities, but obviously we’re very pleased to see other people doing it as well because it shows it’s the right thing to do and it’s the right time to take RAS and scale it up and industrialise it.”
Pure Salmon has chosen Israeli RAS expert AquaMaof as its technology partner and has bought a half share in AquaMaof’s RAS salmon plant in Poland. It has a capacity of just 580 tonnes a year but has already produced 6kg salmon that prove the technology works. The facility will be strategically important as Pure Salmon’s training and R&D centre.
Pure Salmon has also recruited experienced fish farmer David Cahill as its head of production. Cahill’s 28 years of experience includes 18 years with Marine Harvest in Scotland and seven years as general manager aquaculture with Huon in Tasmania.
First harvests in 2022
Work on Pure Salmon’s first new farm, a 10,000-tonnes-per-annum facility in Japan, begins next year, with the first salmon due to be harvested in 2022.
The company also has plans for a 20,000-tonne-capacity facility in the eastern United States, and a 10,000-tonne farm in Europe – either France or Italy.
The Singapore-headquartered company also intends to build five facilities in China, along with more in the US and other regions.
Fothergill points to increasing improvement in technology and the margins that are being made by salmon farmers as reasons why 8F’s partners believe now is the time to invest in RAS facilities.
“Also, we think the whole environmental factor is very important: from sea lice and the other issues with salmon farming, to the fact that a RAS facility can be built where the consumer is, and you don’t have to fly the salmon, which is a major change in the dynamic of the industry.”
He is also undaunted by the fact that RAS grow-out facilities have yet to prove themselves to be price competitive with fish grown in open net pens.
“We think that scale is the answer to making RAS successful and that’s why we’re looking at facilities of 10,000 tonnes and 20,000 tonnes for our projects because there you have the economies of scale throughout the business - from a capital expenditure perspective but also once you’re running it, it helps to make the cost of production lower.
Size matters
“And we need size to be able to sell to large retailers and distributors; it’s very difficult to do that with a very small production facility. It’s also important for the global retailers, to be able to engage with them in different countries and different continents and sell them the same product with the same quality that’s produced in the same manner.”
Pure Salmon isn’t relying on environmentally-conscious customers to pay a premium for its salmon, although it’s hopeful it will get it.
“We’re not building into our financial models a need to sell our salmon at a premium, although we would expect to be able to sell it at a premium because it’s clean, it’s sustainable, it’s fresher, it hasn’t had any chemicals or antibiotics used on it,” says Fothergill, a former senior executive at Deutsche Bank.
He concedes RAS farms are capital-intensive investments but adds: “When you look now at the cost of the cage licences in Norway, for example, suddenly building a RAS facility looks pretty cheap. The cage licences per tonne are going for about double the cost of building one of our new RAS facilities, so it is comparatively economically sound from that perspective.
“But it still requires cash. 8F is an investment management company and we’re raising capital from our investors that we will then deploy in these facilities. That’s how we’ve funded the Japanese facility and the Polish facility that already exists.
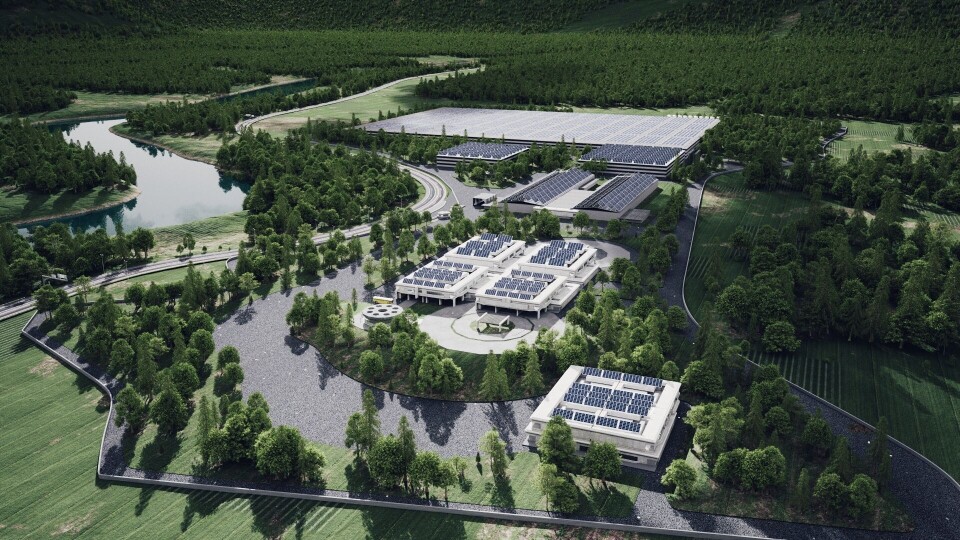
“In terms of raising capital we are looking to raise US$300 million for the first phase of our project, which is the four facilities in Poland, Japan, North America and Europe. That will be 40,000 tonnes.”
When regional grants and some bank borrowing are added in, the total cost of the first phase reaches $500m.
Separate fund for China
8F will establish a separate fund to raise money to invest in China. It is currently looking for locations and working on the second fund.
The figure of 260,000 tonnes was arrived at after 8F looked at where there would be demand. “It could get larger, and obviously as we go along we could get asked to build other facilities elsewhere, so it could rise but that’s our current target,” explains Fothergill.
“Each facility will essentially be the same,” he says. “That’s all part of the scalability. We are effectively building the same factory again and again and again, either 10,000 tonnes or 20,000 tonnes.
“We will do full processing, from egg to the end product.”
Pure Salmon is still in talks with egg providers. “The plan is that we will use more than one supplier, because it makes a lot of business sense to have more than one,” says Fothergill.
Staying cool about energy use
Keeping the water cool enough in warmer countries won’t be a problem, he says. “The AquaMaof technology doesn’t require any seawater, so all of the water is coming from a borehole, ideally, or from the water network. Temperature isn’t going to be such an issue as if we were bringing it from the sea. Because it’s recirculation, once it’s cooled it needs less energy to keep it cool.
“It’s another advantage of the AquaMaof system that the recirculation rate is very high, higher than other RAS technologies, which is all very important incrementally to the amount of energy that’s used and the amount of effluent from the system.”
Pure Salmon won’t be waiting for one plant to be up and running before starting another. “That would take us 20 years,” says Fothergill. “The construction of the new facilities will overlap each other.”
Two years of planning
He stresses that a lot of planning has gone into the project.
“This hasn’t just come from nowhere. We’ve been working on it for two years. A lot of work has gone into this to get us this far.
“We work with each of the local governments where we’re locating to discuss things like planning, getting the water and releasing the water and so on.
“In Europe it’s at the highest levels because there’s a huge amount of interest in us locating. The countries and the regions are very, very keen to welcome us. They want the investment, we create a lot of jobs.”