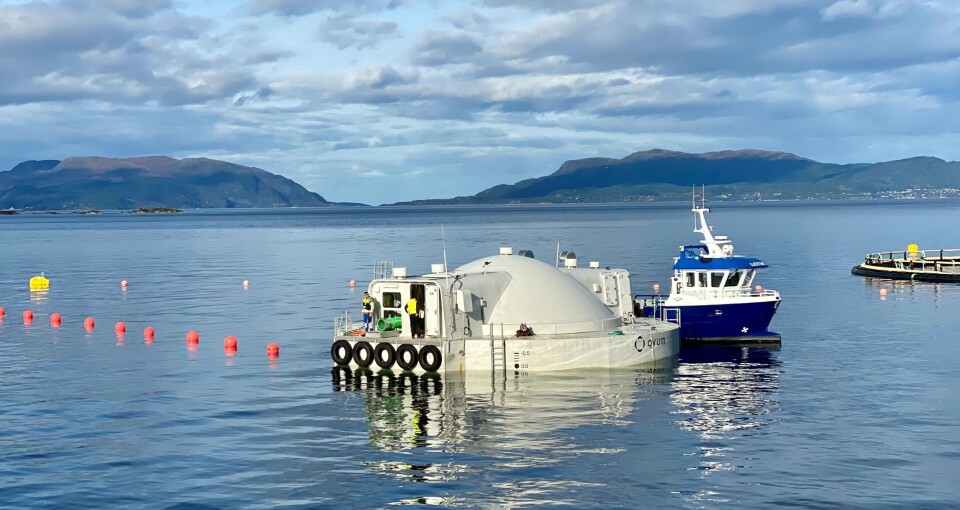
A cracking experience with the MiniEgg
Growth rate, feed utilisation and fish welfare have stood out in post-smolt production in the pilot version of the floating closed containment facility. ‘We are very happy that everything we have learned before scaling up,’ says Siri Vike from owner Ovum.
Fish farming research company Prophylaxia has operated the first Ovum E2000 - or 'MiniEgg' - in Norway’s Romsdalsfjord since autumn 2022, and there have now been two generations of post-smolts reared in it.
“[There has been] a summer and a winter production, and the results have been very motivating for us at Ovum. The final measure of whether our technology is successful is measured in the fish’s performance - and it has delivered,” said Siri Vike, fish health director at the MiniEgg’s owner Ovum, a subsidiary of fish farming technology company Hauge Aqua.
The MiniEgg is a pilot version of Ovum’s Egg, which will be 44-metres high and have 10 times the volume of the 21-metre high MiniEgg’s 1,850 m³.
A couple of weeks ago, the MiniEgg returned to the premises of manufacturer Herde Kompositt, which will make some upgrades.
Larger inlet
“The MiniEgg must undergo an audit. We learned that parts of the bottom section should be adjusted, so now there will be a new bottom cup that includes, among other things, an automatic dead fish system, larger inlet, and better sludge suction,” Vike told Fish Farming Expert’s Norwegian sister site, Kyst.no.
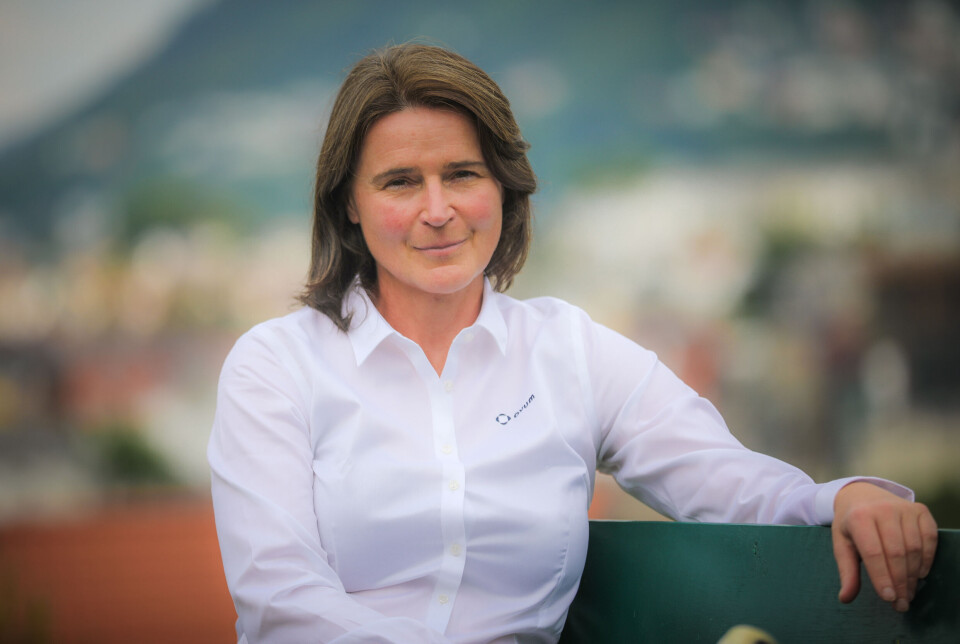
The work is expected to take a few months.
Vike points out that there are three big benefits seen during the production of the first two generations.
“Growth rate, feed utilisation and fish welfare have stood out. On average, the salmon takes five to six months in the sea to reach 1kg. In the MiniEgg, this is 3-4 months. In both rounds we had a feed factor of 0.86 and the mortality was approximately 1.2%. The main reason why the fish died at all is that it jumps into the MiniEgg ‘shell’ and injures itself.”
As a preventive measure, the company has now installed anti-jump skirts.
“The good feed utilisation and fish welfare are mainly due to the stable good environment without handling. The MiniEgg is a training studio for the fish where the water speed is adjusted according to increasing fish length, it has enough oxygen for digestion and growth, enough food and there are no stressors such as lice, boat traffic, predators, etc.”
Among other things, the company uses artificial intelligence-enabled cameras to monitor the fish and document welfare parameters.
A learning experience
Vike says Ovum has learned and adjusted a lot along the way.
“We are very happy about everything we have learned in the pilot before scaling up. The worst day at the MiniEgg was when we had to take out the fish for the first time, then we had not prepared well enough and used equipment that was not adapted well enough. But in the second round we had made the necessary adjustments and we only lost 45 fish (0.1%),” she said.
Something that has surprised the company is the amount of particulate matter that collects in the sludge filter.
“We collect more than theoretically expected, with a dry matter content of up to 15%. This is probably due to good hydrodynamics and the fact that we have a faeces-binding feed recipe,” explains Vike.
Vike said the company is looking forward to getting fish in the MiniEgg again, but it will take a few months before production starts again, as work on the upgrades is in full swing at Herde Kompositt.
“The plan is for the third generation of fish to be placed in the MiniEgg in the summer,” she explained.